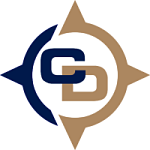
Cone Drive is a manufacturing facility located in Traverse City, MI specializing in worm gear and precision drive technologies. This facility has produced worm gear sets for all branches of the United States military since the early 1920s. The first use of these gear sets began on Navy destroyers and have branched into precision antenna and camera positioning systems.
Samuel I. Cone, founder of Cone Drive, began work in the Norfolk Naval Shipyard as a machinist and draftsman. There, he refined the Hindley Gear – a variant of a worm gear – and patented an improved method of manufacturing the gear. May 1923 marks Cone’s first military implementation, which was on the Clemson class destroyer U.S.S. Case [9] on the chain anchor retracting device. After an extensive trial run on the ship, the gear use was expanded to thirteen additional ships. Michigan Tool Company originally produced Cone’s gears in the 1920s but later a Cone Drive Division was constructed in Detroit. In the 1950s, Cone Drive Division was relocated to Traverse City in an attempt to become more competitive and disassociate themselves from the tool manufacturing environment.
Cone Drive Operations specializes in the manufacturing of double-enveloping worm gear machining. The double-enveloping worm drive offers several distinct advantages over previous gear drives including an increased overall torque load, improved accuracy to the applied load, and a robust design that is second to no other gear. Since Cone Drive Operations conception, they have been working to provide the military and the American industrial complex with cutting edge drive technology. Over the decades, and building on Samuel L. Cone’s legacy, the company has been able to improve upon and refine the double enveloping worm gear. This has resulted in a smaller lighter piece of equipment that’s adaptable to an incredibly wide range of industrial and military applications [2].
To understand the importance of Cone Drive, it must first be established the background of the specific gear drive in question. The history of this type of gear system can be traced back to the ages of Archimedes and Leonardo Da Vinci. During the 3rd century B.C., Archimedes, the renowned mathematician and inventor, had originally invented a screw helix system that was primarily used to pump water out of large sea going vessels that had taken on water. This helical screw system is now commonly referred to as an “Archimedes Screw” or an “Archimedes Helix” [1]. This screw type is still used in many industrial applications, but with a refined name: “inclined screw conveyer”. This screw type is the first stepping stone towards Samuel L. Cone’s double enveloping worm gear drive set. It wasn’t until nearly two millennia later that the next evolutionary step in this technology was established. Leonardo Da Vinci advanced the established “Archimedes Helix” to the next practical and useable level. His engineering skills allowed him to develop the world’s first worm gear drive solution.
Samuel L. Cone now enters the picture of drive solutions in the early 1920s. Mr. Cone’s genius lies in his proprietary manufacturing method of the double enveloping worm gear drive set. An enveloping worm gear is a worm gear where the teeth of the gear and the shaft have been modified to better contact each other and increase the amount of torque transfer from input to load. A double enveloping gear takes that a step further and combines this modified teeth design with a drive (input) shaft with a dynamic radius to better allow for power transfer [3]. Both of these designs are centered on the idea of developing a better mechanical drive system that increases power transfer, precision, and reliability. The double enveloping worm gear design is a very intricate mechanical design that offers a huge engineering challenge that Samuel Cone was able to master and allow his business to flourish.
With the increased efficiency and reduction in cost for the double-enveloping worm gear, and in the midst of a technological revolution of the 20th century, a new realm of possibilities was created for Cone Drive on the battlefield. Successful military technology has to be lightweight, durable, and efficient. Samuel L. Cone found an opportunity in the form of a top-secret prototype aircraft based on a newly-invented form of propulsion: the jet engine.
One component that is easy to overlook but critical to the performance of the aircraft is the mechanism to raise and lower the landing gear in an efficient and reliable method. This was where Cone Drive was able to assist with their double enveloping worm gear technology. The landing gear in front nose gear and the main under belly landing gear were driven using Cone Drive’s gear sets [9]. This top secret aircraft took its first flight on October 1st, 1942, less than a year after the United States had entered World War 2. The Bell XP-59 Aircomet had a myriad of impressive performance traits for the early period of the jet age. The aircraft had a top speed of 413 mph, a ceiling of 46,194 feet (8.75 miles), and a climb rate of 3,200 feet-per-minute. As reference, the famed P-51D Mustang had a top speed of 437 mph and a climb rate of 2739 feet-per-minute. (These stats meant that the Aircomet was a technological wonder of the day, nearly outperforming the already well established propeller driven aircraft) This success would not have been possible without the overall strategy of lightweight durable component design and successful implantation.
The United States and Great Britain began concurrently working on this aircraft as early as mid-1941. On September 8, 1941 it was submitted to the Bell Aircraft Corporation to design and build an airframe for an experimental aircraft for use of the newly invented experimental jet engines [6]. An important note is that this contract was established well before the Japanese attack on Pearl Harbor on December 7, 1941. It is important to note this relationship which further established the United States industrial link to the war before we officially entered the conflict. It is also important to note that the “Lend-Lease Act” of 1940 had already sent the United States on a path leading to full scale involvement in World War 2. In an incredible 368 days the aircraft went from a sketch to taking its first successful test flight on October 8, 1941, with Bell’s chief test pilot, Robert M. Stanley, at the stick. The next day Brigadier-General Lawrence C. Craigie of the United States Air Force took the XP-59 for its second test flight. With the second successful test flight, General Craigie became the first Air Force officer to pilot a jet fighter. With these two simple, or perhaps not so simple, test flights the American and British jet fighter program had begun.
The airframe for the new aircraft was only half of its success. The newly invented jet engine came from the allied Brithish scientists and engineers. In early 1941, the Whittle Company of Great Britain had sent the prototype jet engine to America to be refined and improved. This was taken care of by the General Electric Company. During the next few years, several hundred successful test flights took place, from which the American test pilots were pleasantly surprised by the performance of the first ever jet fighter [6]. This first jet aircraft offered an “unfamiliar simplicity” compared to all of the prop driven aircraft of the day. The lack of the rotating propeller drastically reduced vibrations of the aircraft which made it far more comfortable to fly compared to propeller driven aircraft. With a single propeller aircraft, the prop has a large rotating un-sprung mass. This rotating mass induces vibrations throughout the entire airframe. These vibrations make fighters uncomfortable and potentially dangerous to fly. If the engine speed hits the right speed (rotating frequency), the vibrations can shake the plane to pieces. The new Bell XP-59 eliminated this risk and un-pleasantries of flying.
The Aircomet was a revolutionary step for the United States and Great Britain fighter jet program and laid the ground work for all jet powered aircraft to come. Following the United States victory in Japan, the first Bell XP-59A Aircomet was donated to Smithsonian Institute in Washington, D.C. to be placed on permanent display in 1945 [4]. In this postwar era, it was still acknowledged that this aircraft was the first American fighter that was produced and was a technological wonder. Although Bell’s Aircomet was never put into large scale production, by the end of World War Two, the double enveloping worm gear had made its way into every branch of the military and to nearly every form of industrial production [10].
The double enveloping worm gears application saw no bounds as it made its way into other (non-direct) military applications in American industry. There was a myriad of different applications for the Michigan gear sets that helped the allied war machine keep rolling through the darkest days of the war. The most notable applications for these gears are in metal cutting and forming machinery. In an environment where there is a need for metal cutting, drilling, and forming in a precision manner, this gear set prevailed. Applications like these could be seen in tank and aircraft factories. It was the United States ability to out produce the Axis powers gave the Allies the upper hand. The other main use for these gears was in the mining industry. Applications included rock crushing equipment to extract copper or iron from the rock. These applications were critical for the allies as they were consuming exorbitant amounts of resources for the war movement. In short, the double enveloping worm gear set is a piece of machinery that helps make other equipment.
Cone Drive, and Samuel L. Cone, have proven themselves to be a tremendous asset towards the United States military war effort and they have forever earned their place in history. It is the “behind the scenes” companies and manufacturing facilities such as Cone that drive the industrial complex and allows the United State to out produce its enemies. Cones gears have made their impact across all military whether on the equipment themselves or in the machinery that was used to produce the equipment. They continue to be a “world leader in double-enveloping worm gears” [7] and produce precision gear sets for all branches of the military. Some of these modern military applications include turret drive systems on modern tanks, helicopter search lights, camera positioning on manned and unmanned vehicles, training and simulation devices, winches, and radar installation positioning drive sets [10]. The company has geographically changed since their beginning but still remains in the upper Great Lakes region and continue to be a reliable supplier. Cone Drive has, and continues to have, a large impact on the technical advancement of the United States military.
Primary Sources
- “Archimedes Screw.”Encyclopedia – Britannica Online Encyclopedia.
- “Double Enveloping Technology.”Double-Enveloping Technology. Cone Drive.
- “Enveloping Gear Technology.”Brighthub Engineering. 2012.
- “Here and There: Museum Piece.”FLIGHT 6 Sept. 1945: 251.
- “Meteor F.1.”FLIGHT 27 May 1955: 727.
- “Two Bells: The Bell Aircraft Corporation’s Unorthodox Jet-Propelled Aircraft and Helicopters: No Combination of the Two – Yet.”FLIGHT3 Aug. 1944: 116,117.
Secondary Sources
- “About Cone Drive.” About Cone Drive. Cone Drive Inc.
- “Bell XP-59A Airacomet.” Bell XP-59A Airacomet. Smithsonian. 2015.
- “Cone Drive History.” Cone Drive History. Cone Drive Inc. 2015.
- “Defense Industry by Cone Drive.” Cone Drive Inc.
- Victory, John. “Keeping America in the Air.” The NACA and Aeronoautical Research.
- “Military Pictures” Strategy Place. Strategy World.