The Keweenaw Research Center was founded in 1953 as the Keweenaw Field Station. Since then it has served as a testing grounds for U.S. military vehicles and modifications to ensure reliability and mobility in snow and on ice.
Early History
The Keweenaw Field Station was chosen by the U.S. Army Snow, Ice and Permafrost Research Establishment (SIPRE), a part of the Army Corps of Engineers, in 1953 as a testing ground (13). SIPRE, which later became reorganized and named the Cold Regions Research and Engineering Laboratory (CRREL), was focused on pure scientific research and building equipment necessary to support their research. Before the Keweenaw Field Station location was selected SIPRE was already using the high-quality snow from the Keweenaw peninsula for research in Illinois (1). SIPRE wanted a field station where it was below freezing for more than twenty days in a row and had a high annual snowfall. Several sites in the Keweenaw peninsula were considered potential locations for the Keweenaw Field Station but a collection of weather measurements over the 1952-1953 winter was conducted to find the best location. They concluded that many of the considered sites had similarly ideal weather patterns, but the current Keweenaw Research Center location was chosen since it had the lowest temperatures, it was easy to access, and it was central to the other considered field station locations allowing researchers mobility if they needed a different testing ground (2).
The military saw a need for the Keweenaw Field Station since the Soviet Union had artic warfare capabilities and bordered Alaska making it a potential site for an invasion. Additionally, since the rise of nuclear weapons the importance of Greenland (soon to be home of Thule Air Force base) and other northern sites for the Distant Early Warning (DEW) radar made the U.S. armed forces cold-weather operational capabilities critically important (14). Over time the research conducted at the Keweenaw Field Station changed its focus from pure cold weather scientific inquiries to the testing of vehicles in snow and on ice.
“During its tenure as the SIPRE’s Field Station, Keweenaw served as a test site for elements from the Ordnance Tank Automotive Command, Detroit Arsenal, Land Locomotion Laboratories, Quartermaster Laboratories, General Motors Proving Grounds, Aberdeen Proving Grounds, Waterways Experiment Station and Engineer Research and Development Laboratories. SIPRE’s Permanent staff of 20 employees maintained approximately 100 vehicles at Keweenaw, including tractors, snow plows, and various sizes of trucks and trailers, not to mention experimental models of vehicles undergoing tests.”
Wright, p.15 (14)
The shift in the focus of research at the Keweenaw Field Station to vehicle functionality and maneuverability in cold weather is seen by the large vehicles to staff ratio. Since vehicle testing was not a specific task assigned to SIPRE, compared to pure science questions SIPRE decided to transfer the Keweenaw Field Station. The Keweenaw Field Station was transferred to the U.S Army Mobility Command (ATAC) in 1963 (14). ATAC then transferred the Keweenaw Field Station to Michigan Technological University to research and test military vehicles, other miscellaneous cold weather topics for the government, and civilian vehicle testing (15). ATAC found the Keweenaw Field Station served as an ideal testing ground since it was close to Detroit Arsenal, it received a lot of snow, and it is located in an isolated area.
Vehicle Testing
Vehicle field testing has been a focus of the Keweenaw Research Center. The Detroit Arsenal which is an important part of the ATAC is located within one day’s drive so this makes the Keweenaw Research Center close and convenient for cold weather and general testing (16). Additionally, the Keweenaw Research Center is supported by Michigan Technological University, so it has access to engineers and advanced technology. Historically some projects that have been sent to the Keweenaw Research Center included vehicle testing and consultation. Listed below are several projects that the Keweenaw Research Center impacted.
Hovercraft were tested by the Keweenaw Research Center in the 1970-1971 winter. The Hoverhawk and SK-5 were tested to evaluate the turning radius, hill climbing, and obstacle climbing for winter operations (4). Testing showed that hovercraft had a large turning radius at speeds useful for military purposes, obstacles required slow sped to hover over, and hills with a grade of 20% could be climbed. General observations from the study showed that hovercraft required clear terrain and that the vehicle did not reach its highest potential due to the drivers not wanting to ruin equipment or get injured. This research prevented hovercraft from being adopted for use in arctic warfare. By proving that the Hoverhawk and SK-5 were unsuitable for winter warfare due to a lack of maneuverability, the Keweenaw Research Center prevented the Army from investing in vehicles that conceptually had potential, but would be unable to effectively support soldiers in a combat environment.
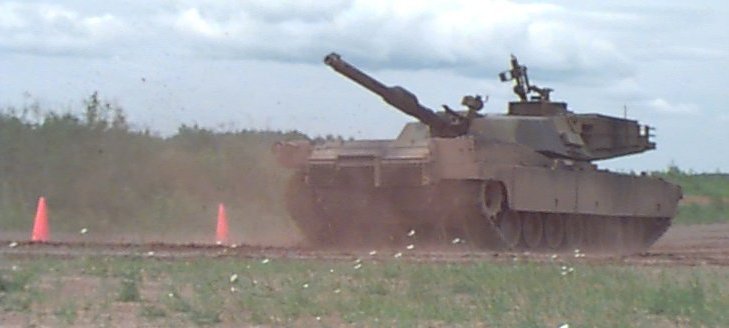
The development and testing of winter vehicle capabilities at the Keweenaw Research Center reached a high note in the early 1980s. The Keweenaw Research Center tested and developed methods to increase tank mobility over ice during the winter of 1981-1982. The testing occurred on the M1 and M1A1 Abrams tanks. The T156 track was tested as a plain tread, with snowshoes, and with tungsten carbide studs. The tank was driven on a test course during the winter and stopping distance, time trials, hills climbed, and traction were tested (5). The study showed that the unmodified tank was ineffective in deep snow or on ice. The performance between tungsten carbide studs versus snowshoes was similar in many instances but the tungsten carbide studs gave the tank slightly better performances (5).
In 1983 the M60 Patton (the tank replaced by the M1 Abrams) had a proposed change in its air filtration system. The M1 Abrams tank was gradually adopted, so the M60 Patton tanks were still being used and upgraded. The Keweenaw Research center was contracted by ATAC to compare the cold weather capabilities of the new filtration system versus the old filtration system. The Keweenaw Research Center drove tanks with each filtration system on a test course while it was snowing, and left tanks in the snow overnight in order to attempt to clog the filtration systems with snow (6). The testing with regards to the filtration system was inconclusive. Each filtration system tested did not get clogged in the snow, so the Keweenaw Research Center was not able to provide a recommendation on which filtration system was better. However, each filtration system had problems with parts freezing during continuous cold weather operations.
Although the tungsten carbide studs were proven to be an effective device to aid tank traction, the army continued tread research since according to former ATAC and Keweenaw Research Center employee Jeff Parks “The Army wants a track that works everywhere, is lightweight, mine proof, quiet, doesn’t damage roads, lasts forever, and is dirt cheap” (7). Tank tracks are key to performance since the traction affects tank maneuverability. The Army has a large number of demands that are conflicting. The metal snowshoes or studs that make a track work on ice will destroy roads. Since no perfect tank track will exist military commanders need to take into consideration the terrain, weather, and civilian considerations to determine which type of tracks will be the best for a mission.
Further research by the Keweenaw Research Center on tank tracks led to the design of cleats for tank tracks (3). Once the Keweenaw Research center adapted a cold room to test tread designs outside of winter they were able to rapidly create major improvements in track design by exposing out bad track designs. The Keweenaw Research Center designed a cleat that allowed an M1 Abrams to climb a 30-degree incline which would help a tank maneuver over steeper obstacles. This would increase the battlefield effectiveness of tanks since the maneuverability of the M1 Abrams would be increased. The long winters in the Keweenaw peninsula and the detailed testing by the staff of the Keweenaw Research Center lead to the Army optimizing the design of the cleats used. This testing improved the Abrams tank series cold-weather operational capabilities.
After the Keweenaw Research Center was done with the cold weather testing of T156 track the Army’s Yuma proving grounds used the Keweenaw Research Center staff in a supervisory and consulting role (8). Yuma was conducting research and development in 1985 to determine how to devise procedures and build equipment to test the wear and tear that typical tank use, such driving at high speeds in rough terrain, will have on the tank track. The Keweenaw Research Center was given an opportunity to view the proposal with ATAC employees and influenced a large research project on the T156 track.
The Keweenaw Research Center has also supported the M1 tank with general engineering support not related to cold weather or snow testing. In the 1990s preliminary research was conducted on the T156 track to detect cracked pins (9). (On a tank track pins hold the individual pieces of tread together.) The Army wanted a reliable way to ensure that the pins were not cracked. Previous tests involved hitting the pins with a hammer and listening to the noise generated, but the test was not considered reliable enough. The Keweenaw Research Center tested the pins using ultrasonic technology. The hammer test was conducted at the same time as a baseline to compare the ultrasonic technology tests too. The study used five people who first used the hammer test, and then the ultrasonic test to find damaged pins in the tank track. The results of the testing indicated more accurate and reliable results are obtainable with the ultrasonic testing technology than the traditional hammer test.
The Keweenaw Research Center was contracted by the ATAC and CRREL to do preliminary research on the Mobility over snow transport (MOST) system (10). MOST is the military term for a snowmobile. The plan for the MOST system was to provide special forces with a rapid and quiet way to infiltrate their area of operations or an objective. The Keweenaw Research Center used a civilian snowmobile to evaluate the noise produced by a snowmobile and offered suggestions on how to improve the MOST project. The key findings were that putting a noise-insulating foam around the engine, track, and a silencer on the exhaust pipe would be a good starting point for the actual research and development to focus on. Since this was low budget feasibility testing dedicated to custom parts, running the equipment to failure, and snow qualities were not taken into consideration. After further inquiries nothing else about MOST was found in the Defense Technical Information Center, indicating that the research was not used or is classified to prevent the replication and prediction of operational capabilities of Special Forces snowmobiles.
Recent Projects
More recent projects by the Keweenaw Research center include the Specialized Compact Automated Mechanical Clearance Platform Roller to destroy landmines and the SnowPaver to support CRREL research in Antarctica. These are recent projects with unclassified details since at least parts of the research conducted has been released to the public whereas some research being conducted could be classified in its entirety.
The Specialized Compact Automated Mechanical Clearance Platform Roller (SCAMP) was tested at the Keweenaw Research Center. SCAMP is a proposed minefield clearing technology that detonates mines by rolling over the landmine and triggering it and is being investigated by the U.S. Army Armaments Research, Development, and Engineering Center (11). SCAMP is mounted to the front of a route clearance vehicle that is driven over a route that needs to be made safe from landmines. This device has use in former war zones where unexploded ordnance is a threat to civilian life and could help US armed forces if there is a mine threat in future conflicts. This would not minimize the remotely detonated improvised explosive device (IED) threat since this technology defeats pressure detonated mines, compared to directly targeting the explosive charge or detonation mechanism. The Keweenaw Research Center provided testing grounds for this technology to prove its feasibility.
CRREL maintains operations in McMurdo Station in Antarctica to support extreme cold weather research. In the early 2010s CRREL was looking to develop a new snow road repairing machine, which would compact snow so that it could be driven over (12). The Keweenaw Research Center developed a machine they called the SnowPaver. The Keweenaw Research Center originally developed the technology in the 1980s while researching snowmobile trails maintenance for the Department of Natural Resources. This is an example of civilian research contracts through the Keweenaw Research Center that have benefited the Army while not many military research topics were being studied at the Keweenaw Research Center. Civilian research in transportation-related fields gave the Keweenaw Research Center experience used to build the SnowPaver at no cost to the military. The SnowPaver was built by the Keweenaw Research Center and sent to Antarctica with Keweenaw Research Center support staff to evaluate the SnowPaver. During the artic testing, the SnowPaver was shown to be a useful tool for some road repairs, but it needed some modifications and improvements to give the performance required but the SnowPaver was adopted.
Primary Sources
[1] Snow Ice and Permafrost Research Establishment Wilmette ILL (1953) “Tests on Snow Beams“
[2] Gerdel, Robert W., Diamond, Marvin. (1953). “Climatological Study of Keweenaw Peninsula”
[3] Blaisdell, George L. (1991). “First International Conference on Winter Vehicle Mobility”
[4] Liston, Ronald. (1971). “Surface Effect Vehicle Engineering Test Procedures”
[5] Smith, R. L. (1982). “M1 Winter Tank Test (Traction Devices)“
[6] Osborne, Mark D. (1983). “M60 Clean Air Winter Test“
[7] Parks, Jeff .” Re: Tank research in the Keweenaw Research Center” Message to Colleen Klausner. Email.
[8] Goldberg, Alfred., Chinn, Diane J., Brady, Robert L. (1987). “Studies on the Testing and Analysis of T156 Tank-Track Shoes“
[9] Laurain, Martin P. (1993). “Track Pin Testing Procedure Hammer Ring Test Evaluation“
[10] Osborne, Mark D. (1991). “Development Of a Kit to Reduce the Noise Level of the MOST Vehicle“
[11] de Brun, Erik., Poff, Scott. (2011). ” SCAMP Anti-Personal Mine Roller Performance Testing“
[12] Shoop, Sally A., Alger, Russ., Kunnari, Joel., Wieder, Wendy L. (2014). “Evaluation of a New SnowPaver at McMurdo Station, Antarctica“
Secondary Sources
[13] Manders, Damon. (2011). Research and Development in the U.S. Army Corps of Engineers: Improving the Common Stock of Knowledge
[14] Wright, Edmund A. (1986). “CRREL’s first 25 years 1986: 1961-1986”
[16] Hartnell, Cameron (2010). Ice Station Keweenaw: The Early History of the Keweenaw Research Center: 1953-1992.
[15] Lankton, Larry D. (1984). “HISTORIC PROPERTIES REPORT: DETROIT ARSENAL AND SUBINSTALLATIONS PONTIAC STORAGE FACILITY, MICHIGAN AND KEWEENAW FIELD STATION, MICHIGAN”